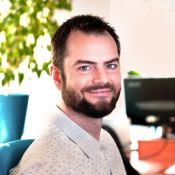
1. Úvod
Mezi nejčastější způsoby aplikací žárových nástřiků patří metalizace neboli šopování, a to pomocí elektrického zdroje tvořícího oblouk nebo pomocí zdroje plynového. V angličtině se pro plynovou metalizaci používá termín „flame spraying“ – nástřik plamenem). Možná jste o těchto procesech slyšeli alespoň okrajově. Znáte ale jejich podobnosti a rozdíly a jaké využití mohou mít? V tomto článku se podíváme na některé z hlavních rozdílů mezi zařízeními obloukovými a plynovými, abyste jim lépe porozuměli, pokud se rozhodujete o pořízení jednoho z nich nebo obojího.
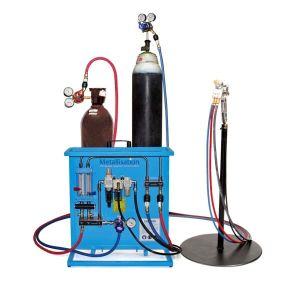
anglického výrobce Metallisation Ltd.
2. Nástřik plynem
Při nástřiku plynem se používá teplo, které vzniká v hořáku metalizační pistole spalováním směsi kyslíku a plynu, obvykle propan-butanu nebo acetylenu. Tam se směs plynů zapálí a vytvoří plamen, který ohřívá spotřební přídavný materiál - buď drát nebo prášek (v našem textu se budeme věnovat drátu). Drát je do pistole navíjen pomocí hnací jednotky v pistoli poháněné stlačeným vzduchem. Roztavený drát je stlačeným vzduchem “atomizován” na drobné částice a rozprašován na povrch, na kterém pevně ulpí převážně pomocí mechanických vazeb a vytvoří ochrannou vrstvu – povlak.
Pořizovací náklady na plynovou metalizaci jsou zhruba třikrát nižší než pro nástřik elektrickým obloukem, ale provozní náklady (zejména nákup plynů a stlačeného vzduchu) jsou naopak vyšší než u obloukové metalizace, jelikož u oblouku se platí především za elektřinu a stlačený vzduch. Při nástřiku plynem se v pistoli taví jeden drát – produktivita nástřiku je tedy dvakrát až třikrát menší než u oblouku, což se projeví zejména u nástřiku větších ploch.
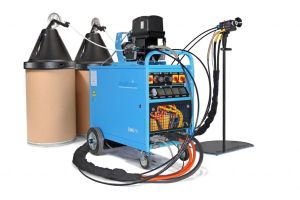
anglického výrobce Metallisation Ltd.
3. Nástřik obloukem
Oblouková metalizace používá elektrický oblouk jako zdroj tepla k roztavení kovových drátů. Podobně jako u plynu se k rozprašování roztaveného kovu používá stlačený vzduch. Zjednodušeně řečeno je elektrický oblouk vytvořen nabitím dvojice drátů opačnými náboji a přiblížením konců dvojice drátů skrz trubice v metalizační pistoli. Mezi opačně nabitými dráty dojde k tzv. napěťovému průrazu (vyrovnání nerovnováhy nábojů) a vytvoření stabilního elektrického oblouku. Tento proces se označuje jako TWAS (Twin Wire Arc Spraying – obloukový nástřik dvojící drátů).
Pořizovací náklady na stříkání elektrickým obloukem jsou vyšší než náklady na stříkání plynem, ale provozní náklady jsou nižší. Díky použití dvojice drátů a vyšší rychlosti nástřiku lze dosáhnout vyšší produktivity než u zařízení plynového.
4. Podle čeho si tedy vybrat zařízení
Kromě již zmíněných pořizovacích nebo provozních nákladů bychom se měli rozhodovat podle dvou hlavních kategorií – technických požadavků a osobních preferencí.
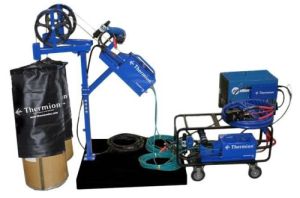
amerického výrobce Thermion Inc.
4.1 Technické požadavky
Některé povlaky aplikované elektrickým obloukem mají vyšší přilnavost povlaku k povrchu než po nástřiku plamenem. Pokud Vaše aplikace vyžaduje přilnavost 10 a více MPa, pak byste měli zvolit obloukový nástřik. Z tohoto důvodu je v některých požadavcích investorů přímo specifikováno, že povlaky musejí být nanášeny elektrickým obloukem. Nicméně i přilnavost povlaku k povrchu po plynovém nástřiku dosahuje často vyšších hodnot než je definováno v požadavcích.
Dalším praktickým důvodem může být mobilita zařízení, ovšem zde si musíme jasně definovat srovnávací parametry. Pistole s hadicemi pro plynovou metalizaci je snáze přenosná než kompletní vybavení pro obloukovou metalizaci. Nicméně pokud uvažujeme manipulaci s plynovými lahvemi a povinnost dodržovat bezpečnostní předpisy pro práci a manipulaci s tlakovými láhvemi, můžeme naopak obloukovou metalizaci označit jako tu mobilnější.
Dalším důležitým technickým hlediskem je požadovaná rychlost nástřiku, kdy nástřik obloukem je mnohem produktivnější než plyn. Například hodinová spotřeba drátu pro plynový nástřik zinku je kolem 10 kg ve srovnání s obloukem, který může být dokonce vyšší než 50 kg/h. [1]
V neposlední řadě je pak třeba definovat velikost metalizovaných dílů. Pokud se jedná o malé díly nebo plochy o malé šířce a/nebo o nástřik členitých konstrukcí, doporučuje se spíše plynové zařízení. Díky tavení jednoho drátu určitého průměru má menší rozptyl nástřiku a tedy menší odpad drátu (tzv. prostřik). Plynové zařízení je vhodnější i tehdy, pokud se chystáte metalizovat jen občas pro své vlastní potřeby ve své dílně.
Pokud jsou součástí Vaší aplikace větší díly s výměrami v desítkách až stovkách metrů čtverečních, např. mostní a jiné ocelové konstrukce, je na místě výběr obloukového zařízení, které využívá tavení dvojice drátů. V tomto případě minimální potřebný výkon zařízení závisí na průměru dvojice drátů. Rovněž byste měli vědět, do jak míry má být zařízení mobilní. Uvedeme příklad: zařízení nastavené na použití drátu o průměru 1,6 nebo 2,3 mm je jakýmsi kompromisem mezi plynovou a obloukovou metalizací. Hodí se i na opravy již provedených nástřiků. Pro tyto jednotky se používají dráty na cívkách a jednotky lze pohodlně převážet. Zařízení nastavená pro průměr drátu 3,17 a 4,76 mm jsou nejefektivnější pro větší plochy. Tady je na místě se rozmyslet, zda budete používat drát na cívkách (častější výměna spotřebovaných cívek), nebo zda zvolíte variantu drátu ve velkoobjemových sudech (možnost delšího nepřetržitého nástřiku, menší odpad nespotřebovaného drátu). Nevýhodou může být hmotnost potřebné dvojice sudů (až 500 kg) a nutnost pevné rovné podlahy pro případný pojezd zařízení. [2]
4.2 Osobní preference
Zatímco z technického hlediska je výběr zařízení často výslovně předem dán, z pohledu osobních preferencí se často jedná o subjektivní pocity a důvody. Někteří lidé prostě neradi pracují s plyny a otevřeným plamenem. Při provozu je třeba se více zaměřit na hodnocení rizik, bezpečnost a pojištění. Kvalitní plynový nástřik vyžaduje poněkud více dovedností než nástřik obloukem (i když těchto schopností lze dosáhnout pomocí tréninku), kromě zdroje stlačeného vzduchu však pistole neobsahuje žádné elektronické součásti, je tedy jednodušší na údržbu a servis. Nástřik obloukem je fyzicky náročnější, zařízení je robustní a těžké. Díky svému výkonu je vyšší spotřeba drátu a bohužel i množství zplodin při nástřiku. Na druhou stranu obloukový nástřik lze také aplikovat při nižší teplotě (zařízení Precisson Arc od amerického výrobce Thermion Inc. pracuje na Aljašce běžně při teplotách -20°C) a na jeho použití nejsou nutné žádné hořlavé plyny. Pravděpodobně je to jednodušší volba, pokud hledáte rychlý a snadný nástřik velkých ploch. Nástřik složitých konstrukcí je zase jednodušší pomocí plamene.
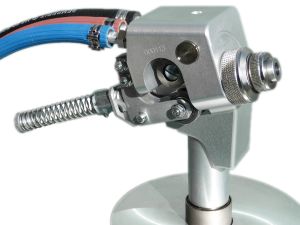
acetylénem
5. Příklady použití nástřiku plynem
Drobnější a menší díly; dlouhé, ale úzké plochy; členitější konstrukce jako např. ploty, brány, zábradlí, šasi, disky kol, statory atd.
Výhody plynového zařízení
- pořizovací cena je nižší než u obloukové metalizace
- zařízení je jednodušší na obsluhu i údržbu
- lze stříkat menší členité díly a konstrukce - vysoká depoziční účinnost
- nižší pórovitost
- méně hlučné
Co je třeba brát v potaz
- náklady na provoz jsou naopak vyšší než u obloukové metalizace
- méně mobilní (v případě, že převážíme i tlakové nádoby s plyny)
- některé pistole jsou těžší než pistole pro obloukový nástřik
- stejně jako u nástřiku obloukem je potřebné zaškolení a oprávnění pro práci s plynovou metalizací dle normy ISO 14918
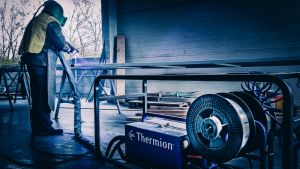
6. Příklady použití nástřiku obloukem
Střední a větší díly, rovné souvislé plochy jako např. ocelové konstrukce, svařence, návěsy nákladních aut, statory, disky, karoserie atd.
Výhody
- elektro oblouková metalizace má nižší provozní náklady než metalizace plynem
- vysoká produktivita nástřiku a větší přilnavost k podkladu díky vyšší teplotě tavení částic
- zařízení je těžší, ale na kolečkách – je tedy mobilní
- pistole se snadno spouští, nemusí se neustále zapalovat plamen křesadlem
Co je třeba brát v potaz
- pořizovací náklady jsou vyšší než u plynového zařízení
- cívky a sudy je nutno kupovat ve dvojících
- spotřeba drátu je mnohem vyšší
- u menších a členitých konstrukcí bude větší odpad neuchyceného drátu na podklad z důvodu tzv. prostřiku
- je potřebné zaškolení a oprávnění pro práci s obloukovou metalizací dle normy ISO 14918
7. Srovnávací tabulka [2, 3, 4]
Aplikace plynem | Aplikace obloukem |
---|---|
aplikace nástřiku lze provádět ručně i strojně | aplikaci nástřiku lze provádět ručně i strojně |
přídavný materiál ve formě drátu | přídavný materiál ve formě drátu |
použité plyny – kyslík + propan-butan/ acetylen | napětí oblouku 20 – 40 V, proud 40 – 650 A |
pracovní tlak plynů:
| tlak stlačeného vzduchu 5 – 7 bar |
průtok stlačeného vzduchu 1,1 – 2,0 m3/ min | |
teplota plamene přes 3000 °C | teplota plamene 3000 – 6000 °C |
průměr drátu nejčastěji 2,5 – 3,0 mm, může být i 3,15 a 4,0 mm | průměr drátu 1,6 – 5,0 mm |
teplota roztavených částic cca 2500 °C | teplota roztavených částic 3800 – 4000 °C |
rychlost částic 50 – 80 m/s | rychlost částic 50 – 150 m/s |
vzdálenost nástřiku 50-200 mm | vzdálenost nástřiku 50 – 200 mm |
tloušťka vrstvy > 50 μm až 3 mm | tloušťka vrstvy > 50 μm až 3 mm |
výkon až 10 kg nataveného drátu za hodinu | výkon až 50 kg nataveného drátu za hodinu |
přilnavost (adheze) 7 - 18 MPa | přilnavost (adheze) 10 – 80 MPa |
porozita 10 - 15 % | porozita 10 – 20 % |
obsah oxidů vysoký | obsah oxidů střední |
Použité zdroje
[1] Ambrož, O. - Žárové nástřiky a jejich průmyslové využití, Praha, SNTL, 1990.
[2] Zinc and zinc alloy wire - ZM Silesia SA
[3] Pawlovski, L. - The Science and Engineering of Thermal Spray Coatings, Chichester, John Wiley & Sons Ltd, 2008.
[4] Analysis of Wire Arc Spraying Process variables on coatings properties - Gedzevicius, I., Valiulis, A.V. , 12th International Scientific Conference, Vilnius, 2009.
Ozvite sa nám
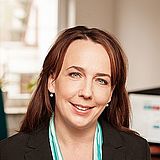
Mgr. Radana Brábníková
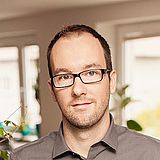
Ing. Pavel Medvec
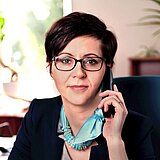
Alena Valchařová
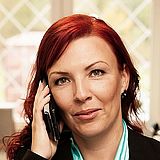
Renáta Sabolová
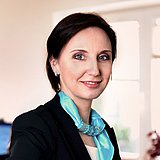